真空成形について
真空成形とは
真空成形とは、ロール巻きされたシート状の材料(基本的にはプラスチック)を熱で軟化させ、真空孔と呼ばれる微細な穴が空いた金型に吸い付けることで、材料を立体化させる成形方法です。
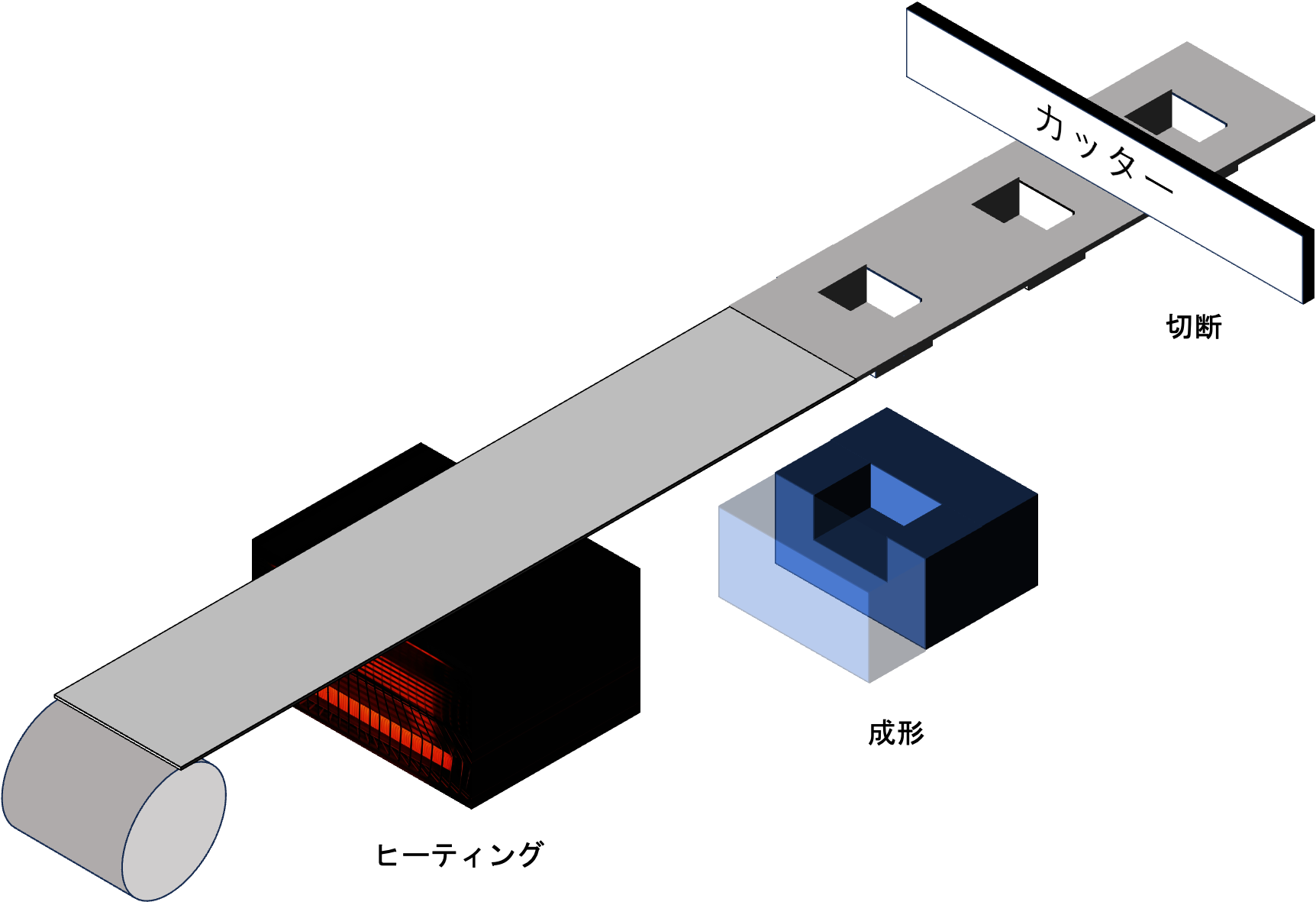
真空成形ラインイメージ
加工工程
ヒーティング
材料に熱をかけ、成形が可能となるように柔らかくします。
温度は材質や厚みによって異なりますが、300℃〜500℃で加熱を行います。
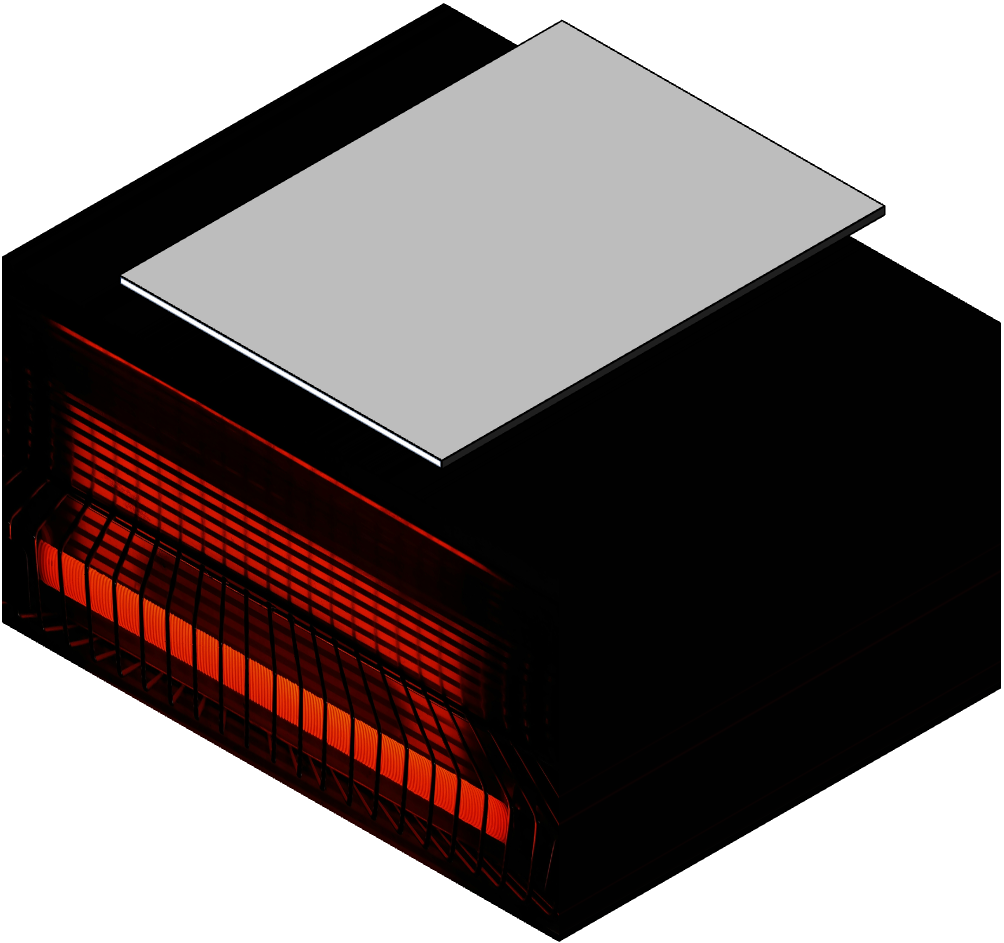
ヒーティング
成形
金型に無数に空いた真空孔を通して、軟化させた材料を真空引きします。
必要に応じて上側からプラグで押し込むことで、しっかりとした形状を出していきます。
材料は金型にピタリと吸い付けられることで、立体化されます。
この工程1回を1ショットとカウントします。
生産性upのため、この1ショットで数枚のトレーをまとめて製造することが多いです。
1ショットで4枚のトレーを成形する場合、1ショットあたりの取り数は4となります。
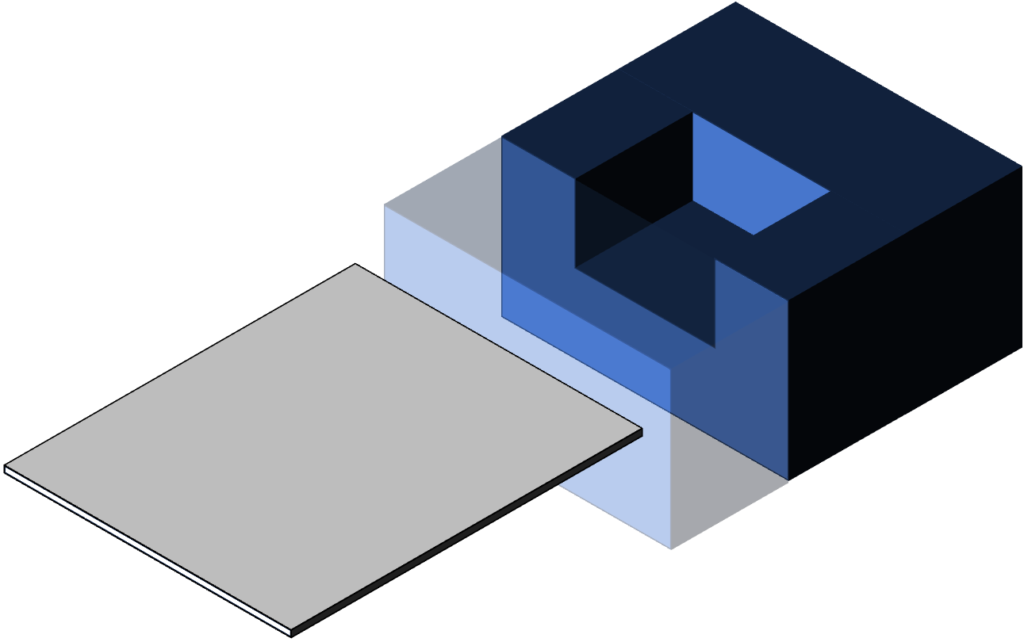
ヒーティング材料送り(自動)
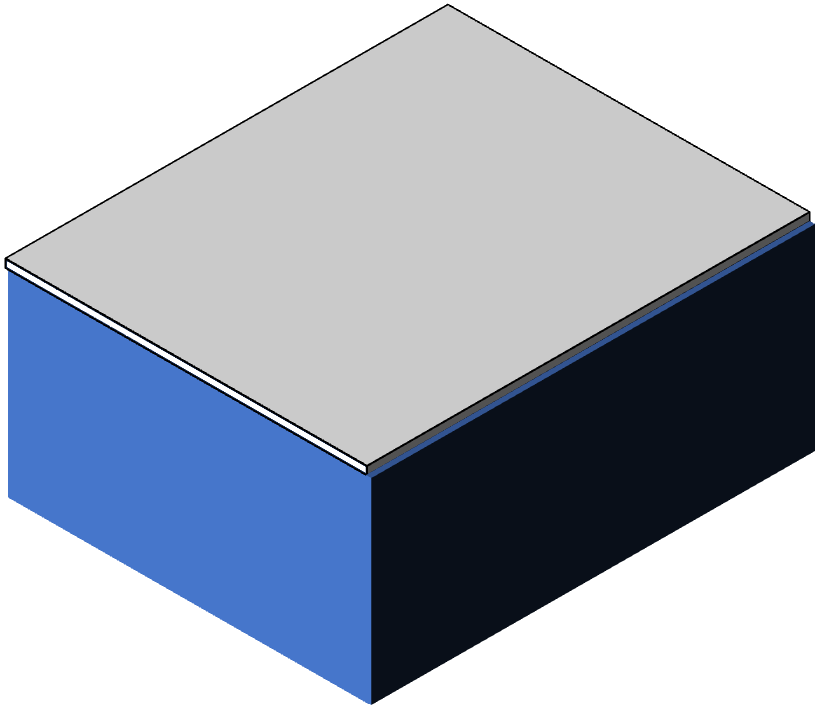
真空引き前
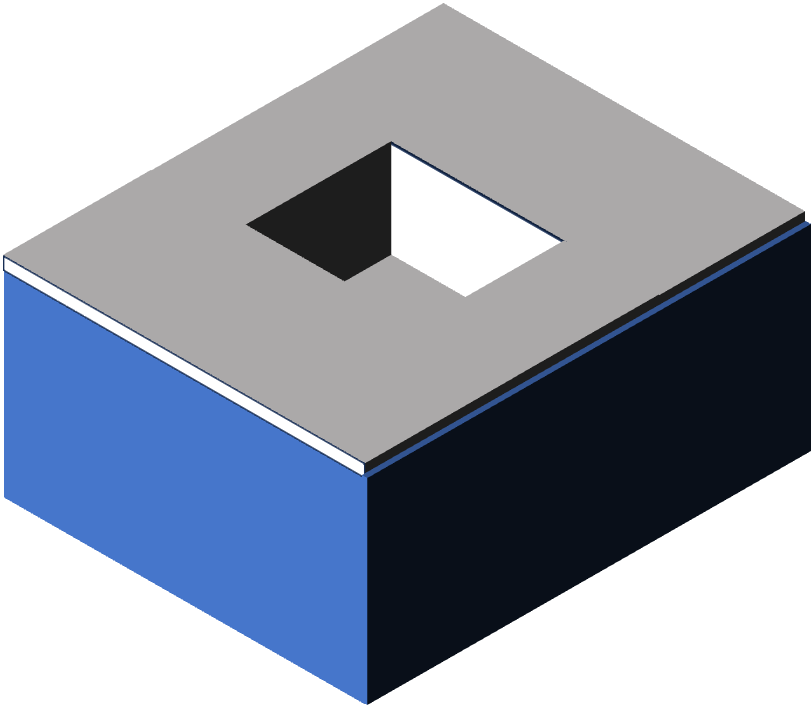
真空引き後
離型
成形をして完了ではありません。成形後に問題なく金型から剥がす必要があります。
しっかりと冷却し、優しく金型から剥がすことで要求品質にあったトレーに仕上げます。
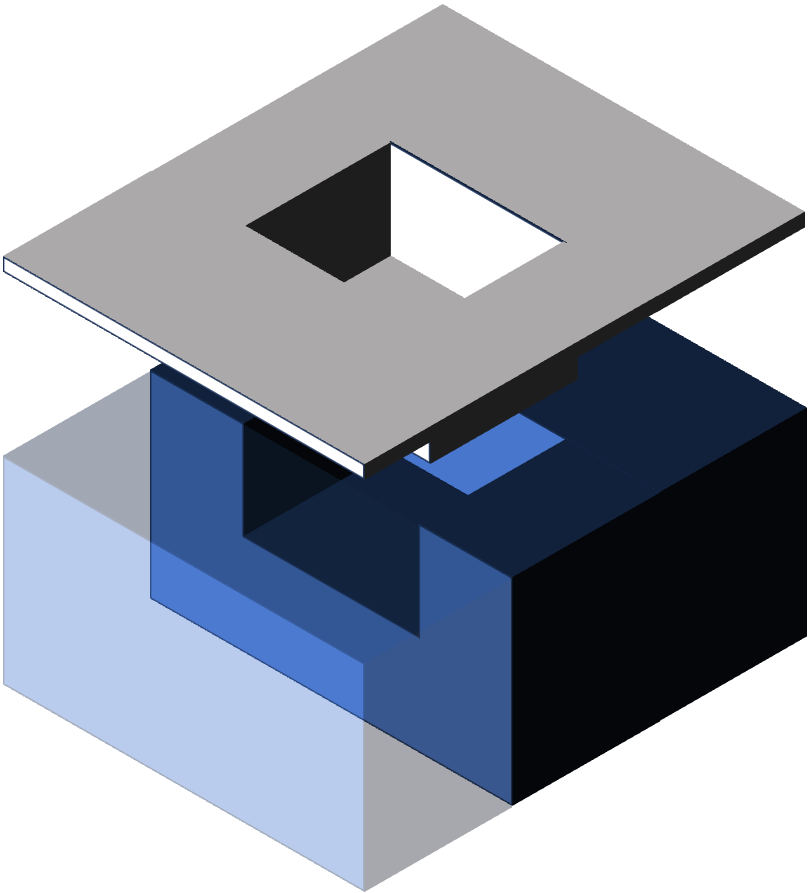
離型
切断
ロール状の材料を連続して成形すると嵩張ってしまいます。
そのため、成形機の最後に1ショット分ずつ切断を行います。
切断された製品は丁寧に重ね、次のプレス工程を待ちます。
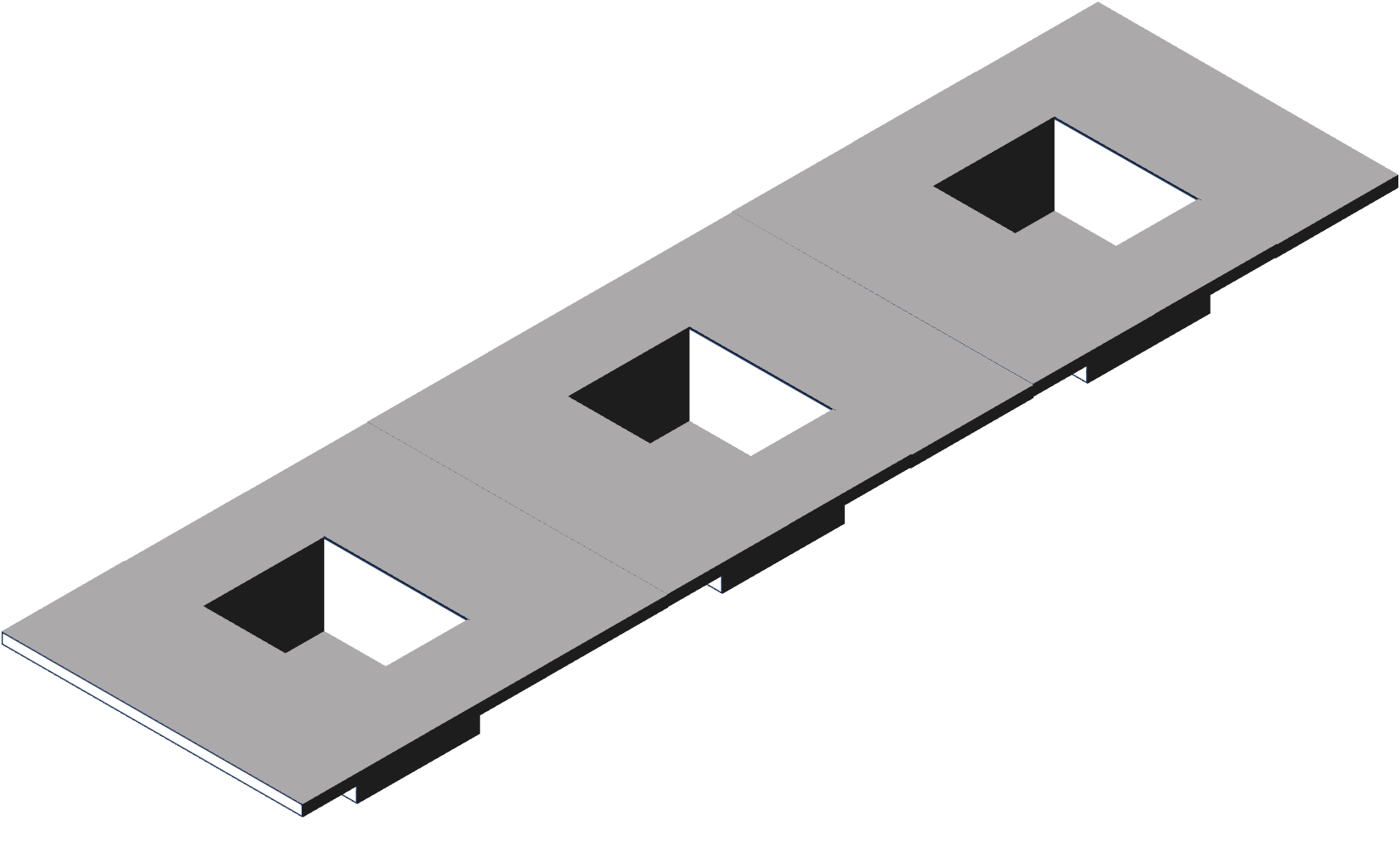
切断前
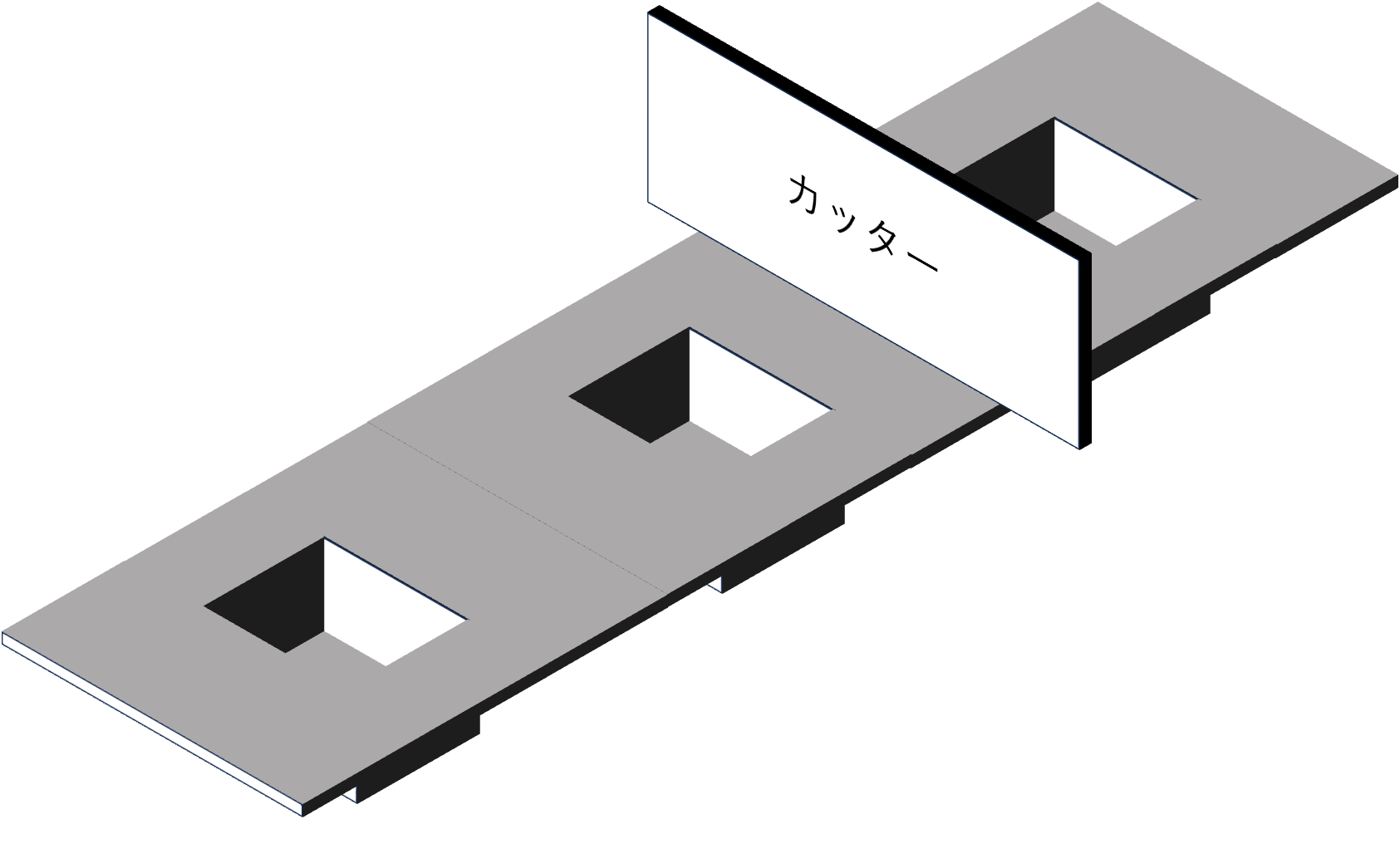
切断
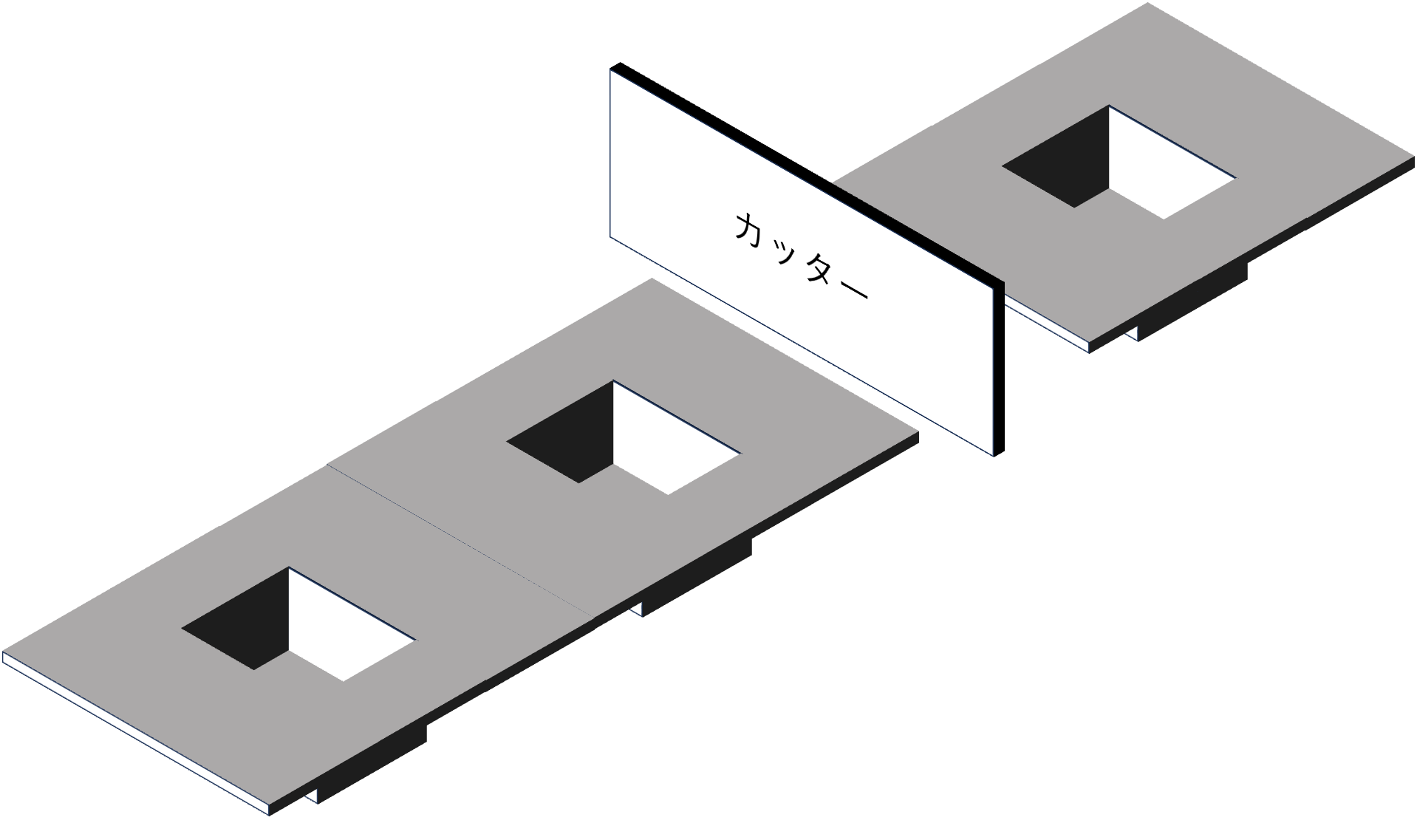
切断後
プレス
成形・切断をするだけでは、お客様が求めるトレーは完成しません。
成形した周囲の不要な部分を切り落とす必要があります。
プレス工程では、お客様が求めるサイズの抜き刃を使用し必要な部分のみを切り取ります。
その際に発生する不要な部分は、リサイクルに回っていきます。
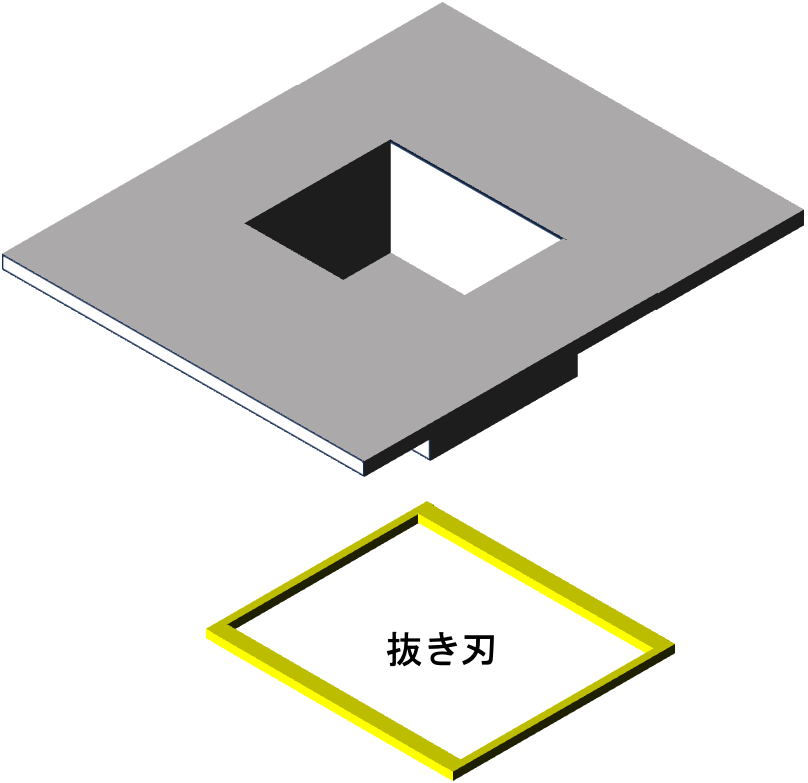
プレス前
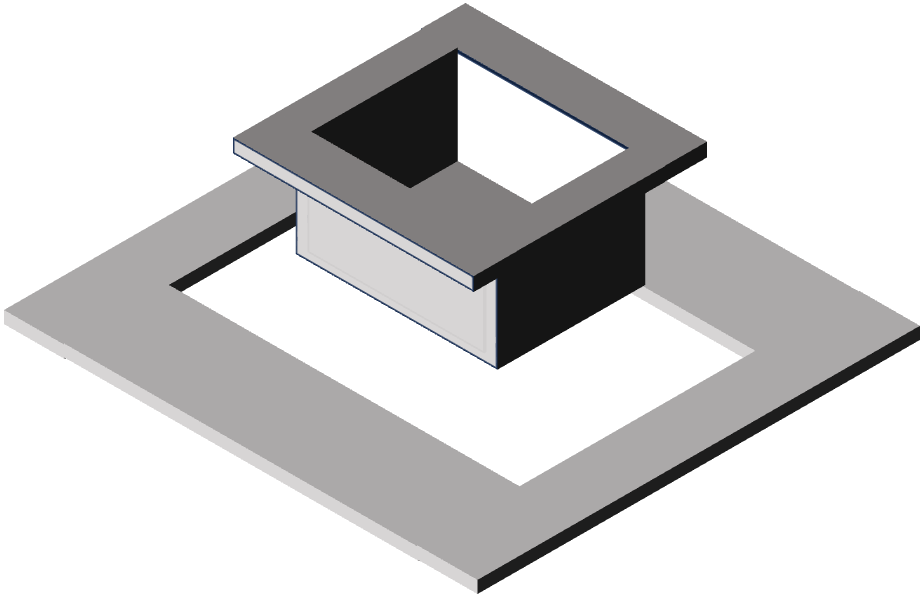
プレス後
検査
真空成形は、様々な要因によって品質が変わるため、検査工程がとても重要です。
例えば、気温や湿度、ロールごとに異なる材料のクセなどの要因が挙げられます。
突発的なシワや薄い部分の発生など様々な不具合を熟練の技術とITを駆使して見つけ出します。
梱包
どれだけ生産を行なっても、お客様の手元に届いた際に破損していては意味がありません。
お客様に到着した際の品質と最適コストを実現する梱包効率の両方を求め、梱包を行います。